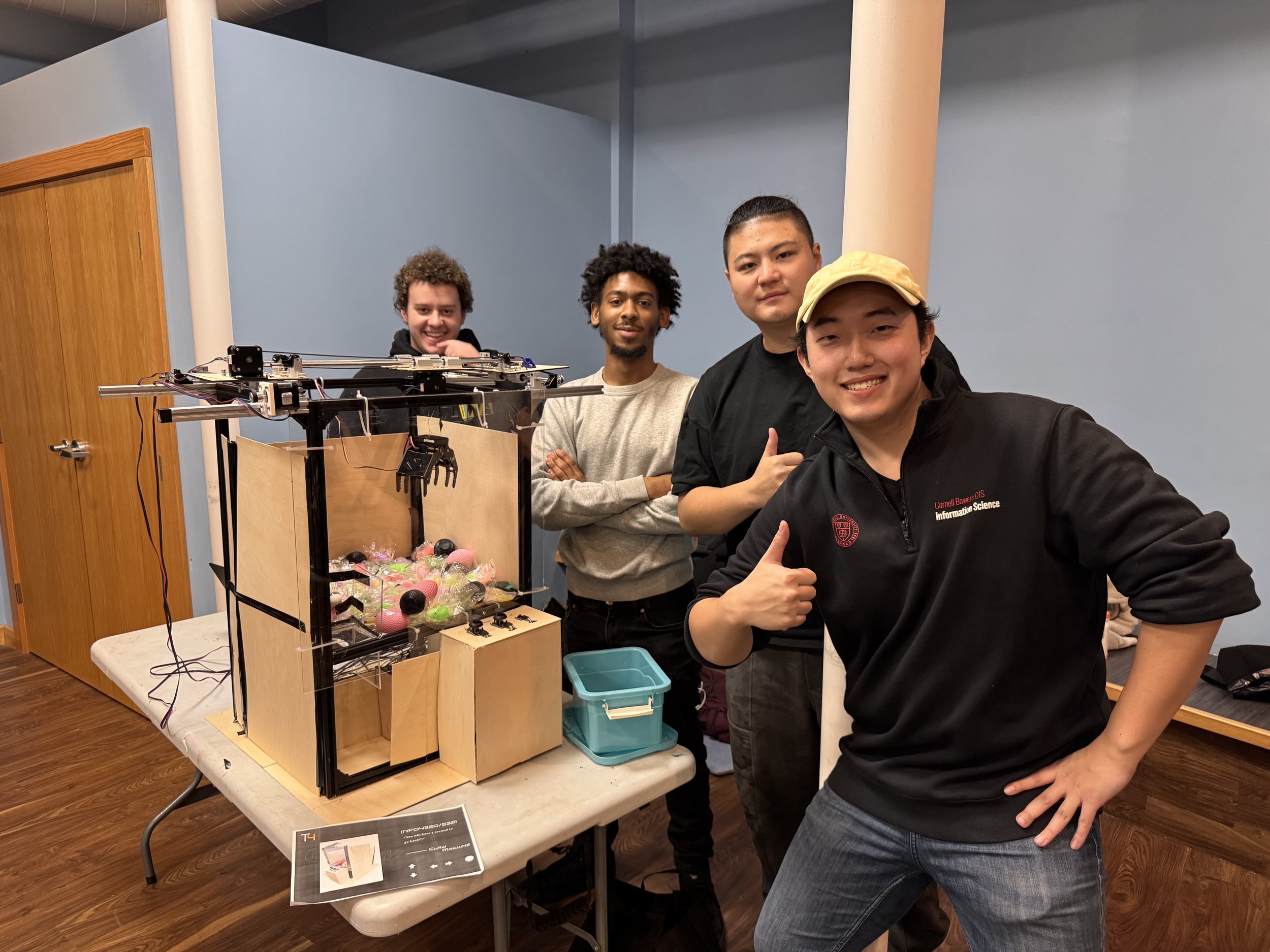
Claw Machine
Date: September 2024 - December 2024
Tags: Interactive Technology, Physical Computing, Hardware, Tangible Interface Design, Rapid Prototyping, Laser Cutting, 3D Modeling/Printing
YouTube: Claw Machine Demo
PDF: Claw Machine Report
As a team of four, we built a claw machine with materials bought on a budget of $300 using arduino and the esp32 adafruit feather. This project involved creating a claw machine that’s not only fun to play, but also more fair and easier to use, especially for younger audiences. We sought out to offer an enjoyable experience that keeps the excitement of the classic game but makes it more accessible and user-friendly.
Sketch + Features ✏️
We started with a series of rough sketches and prototyping plans to visualize how the user would interact with the machine, and how the internal mechanics would support the gameplay.
Claw Mechanism 🤖
A simple but sturdy 3-pronged claw powered by a motor and controlled using fishing wire. Designed for smooth opening and closing without requiring advanced servo calibration.
Rail Movement System 🚆
Built on a 2D axis, the claw travels across X and Y rails using belt-driven motors. The claw can reach any area above the prize field for optimal game coverage.
User Input Interface 🎮
A large arcade-style joystick and single button allow even young users to control movement and operate the claw without confusion.
Parts + Materials 🔩
We sourced low-cost and recycled materials where possible:
Metal Frame
Wood Platforms (Laser Cut Plywood)
Acrylic Front Panel
Claw + Motor (Fishing Wire Tension-Based)
Motors + Belts for Movement
Joystick + Button
Hot Glue, Screws, Tape, Zip Ties
ESP32 Feather + Arduino-compatible Board
Assembly 🛠️
Frame Construction 🧱
The outer frame and toy drop platform were built using laser-cut plywood, held together with screws and glue.
2D Axis Rail System 🔄
We mounted the motor-driven belts to rails using 3D-printed holders to allow controlled movement of the claw along the X and Y axes.
Claw Setup 🪝
The claw was suspended via fishing wire, with a motor controlling the winding mechanism to raise or lower it.
Input Interface 🎮
The joystick and button were mounted on an accessible front panel for intuitive control.
Fun with the Kids 🧒
Once built, we brought the machine to the Ithaca Science Center for kids to test the game — and it was a hit! They found the controls simple, the claw responsive, and the game rewarding. By balancing the claw's grip and improving win chances, we ensured more delight and less frustration.
Looking Back 🔍
Challenges ⚠️
Wiring limitations: We originally had limited analog input pins, which made it difficult to run the joystick and button simultaneously.
Motor tuning: Getting the claw motor to respond with the right strength and timing took trial and error.
Structural alignment: Even small shifts in belt tension affected movement precision.
What We’d Do Differently 🔧
Use a more efficient board layout to better support analog/digital input combinations.
Refine the claw release mechanism for more precision.
Add a restart button or round-based timer for replayability.
“Not an engineer... yet.” 🙃
This project taught us a ton — from the intricacies of physical computing to the importance of user-centered design, even when working with physical objects. Most importantly, it was fun.
What We Learned 🧠
Designing for simplicity leads to more engagement
Physical builds require more iteration than expected
Tangible interfaces are powerful — when thoughtfully designed, they transcend age and skill barriers